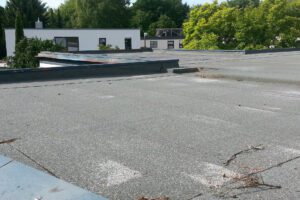
The renovation of a felt-covered roof is often overlooked, which subsequently affects the quality of the roofing. When deciding on a renovation, it’s important to not only consider the waterproofing aspect but also the correct sequence of tasks.
A felt roof renovation is often essential after just a few years of use. Though older buildings might not be renovated for longer periods, eventually significant wear and tear develop on the roof’s surface. The result is leaks and often much higher costs than if immediate renovation was undertaken. With felt roofing, it’s always better to prevent problems than to fix them later. The same goes for renovation: better to attend to it sooner rather than too late.
A significant challenge when renovating a felt roof is the dismantling of specific elements – roofing in eaves strips, slope regulation, and damaged areas. Modernising many buildings also involves the removal of galvanised sheet metal fittings, gutters, downpipes, and lightning protection systems. Equally important is the sequence of tasks related to preparing the base for felt roofing. It’s crucial to meticulously clean the surface, get rid of characteristic blisters, or trim any irregularities. A typical roof renovation may also require sticking down the edges of the existing cover, especially protruding old felt elements. Proper impregnation quality is vital. The base, in this case, is protected with a special asphalt emulsion.
Beyond the tasks related to laying the felt, roof renovations often require additional activities such as sheet metal fittings, the creation of drain tanks, or even painting works aimed at anti-corrosion conservation.
A repair is primarily necessary when there are visible cracks and blisters on the surface. While one can opt for ongoing repairs, patching up with more pieces of felt spoils the aesthetics and doesn’t provide the efficiency that more modern renovation technologies offer. It’s also worth noting that if the roof covering consists of several layers of successively applied felt, the next layers require the removal – and thus costly disposal – of the previous ones.
If one notices defects on the roof – the aforementioned blisters or clearly delineated cracks tending to form an entire network of leaks – felt roof repair must be undertaken promptly. However, even with a quality covering, it’s worth carrying out protective conservation.
Roof repair, due to the immense technical work associated with laying felt, its potential disposal, and additional tasks, is often seen as a necessary evil. This is a misconception; a roof renovation doesn’t have to involve a complicated scope of actions. HYDRONYLON® – a liquid membrane that forms a seamless layer on the roof – offers a solution. This renovation method proves to be a better solution, especially in terms of quality and speed of execution.
The nature of felt means that even if it’s of lower quality or cracked due to sun exposure, it works excellently as a base for a new protective layer. This material, based on waterborne polymer resins, can be used for both renovating existing roofing and creating new ones in newly built structures. It’s also worth noting that HYDRONYLON® doesn’t require the disposal of existing felt.
Renovating a felt roof, depending on its size, can be very time-consuming. When it’s necessary to remove the old covering and insulation, the renovation can significantly extend. However, with the liquid mass that forms a seamless, flexible, and durable coat, the renovation is much faster. Coating the felt base is possible in just two days. With a drying time for HYDRONYLON® at 22 degrees Celsius and 50% air humidity being less than two hours, and considering the recommendation of at least two layers on the roof with a 12-hour break in between, two days of work should fully suffice to secure a standard surface.