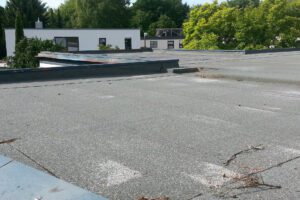
Eliminating potential threats, effective adherence to surfaces, a high degree of safety while maintaining environmental standards – roofing with torch-on felt meets these criteria, but only with the application of appropriate waterproofing.
A good roofing material must combine several elements; it’s always a derivative of quality, cost, and protection effectiveness. Popular torch-on roofing felt – the cheapest solution, though also associated with a relatively higher risk of quality degradation – has long been considered optimal roofing. Various types and broad application possibilities mean that this type of felt is used on both flat and sloping roofs. However, its structure sometimes has points that can significantly reduce its effectiveness.
Torch-on insulation felt, consisting of several layers – from bituminous to reinforcing – loses its properties over time. This can lead to leak threats. A top layer of felt, weakened by intense sunlight and moisture, no longer acts as an effective barrier to water. The fastening itself – through thermal activation, welding, or gluing – then loses its bonding properties, increasing the risk of individual elements becoming unsealed.
The price of torch-on roofing felt shouldn’t be its main selection criterion, but its properties – resistance to tearing force and elasticity. Depending on the type of weave, roofing felts can differ significantly – glass fibre veil by about 2-4%, but polyester non-woven fabric can achieve properties even ten times higher.
The modification of torch-on roofing felt is also essential – its resistance parameters to flow or reactions to lowered temperatures. So, how do types of torch-on roofing felt stack up? High-quality materials marked as SBS – more durable than, for example, APP – maintain their properties for at least a decade. However, materials of this class were not and are not a common standard. Many types of torch-on roofing felt lose quality over time.
Regardless of the type of felt on the roof and how it’s attached, the applied waterproofing sealant is particularly important. For newly constructed buildings, a good-quality coating ensures that the roofing protection effectiveness will be higher. In older construction, where materials with significantly weaker parameters than current ones were often used, waterproofing is an excellent form of roof conservation.
Proper moisture insulation is crucial for the condition of the building – regardless of its age or history. Felt, specialist roofing membranes, or vapour barrier films should be especially protected at the junction with the building’s structure. There’s also increasing attention to the issue of limiting the risk of local coverage damage. Films – and to a lesser extent felt – can be exposed to natural damage, e.g., due to branches located above the roof or in case of hail.
Modern construction trends and the tendency to protect roofs incorporate HYDRONYLON®. Its liquid form and ease of application mean it can be used for both roof renovation and ongoing conservation work and for immediate protection of newly constructed buildings. The absence of seams and excellent complementary properties ensure that this membrane provides the highest degree of accessibility to hard-to-reach places. Critical areas are secured by the HYDRONYLON® layer just like the basic roofing structure, preventing attic dampness.
HYDRONYLON® is applied as a coating in a liquid consistency, which, after acquiring a solid structure, protects roofs made of felt, metal, and membranes. At the same time, it remains fully neutral to atmospheric conditions. Thanks to its technological properties, its tightness remains unchanged. It also positively affects the building’s thermal insulation. The durable structure of the cured HYDRONYLON® set is independent of ultraviolet rays. By reflecting UV, it protects the roof from excessive heating, which is especially important for premises located on the highest floors – typically naturally exposed to above-average sunlight.
Torch-on roofing felt insulation is performed as waterproof insulation. It is attached to a primed substrate. Torch-on roofing felt insulation brings a new dimension to insulation. Previously, horizontal foundation walls’ insulation was made using two layers of asphalt felt, laid on tar. This method is now being replaced by torch-on felt. It is usually laid after pouring the concrete floor slab of the ground floor. We remind and warn you to clean and dust the ground floor before starting to insulate with torch-on felt!
It’s not easy to protect a horizontal surface from the effects of water. The materials used for this should be well-chosen and must have appropriate properties. Investors often opt for torch-on felt. Torch-on roofing felt – horizontal insulation should be laid on a cleaned surface. It should be well heated to adhere properly to the base felt. If we want the felt to retain its properties for longer than a decade, its surface can be treated with our liquid product!